1. Test teorico e analisi
Dei 3valvole dei pneumaticicampioni forniti dall'azienda, 2 sono valvole e 1 è una valvola non ancora utilizzata.Per A e B, la valvola non utilizzata è contrassegnata in grigio.Figura completa 1. La superficie esterna della valvola A è poco profonda, la superficie esterna della valvola B è la superficie, la superficie esterna della valvola C è la superficie e la superficie esterna della valvola C è la superficie.Le valvole A e B sono ricoperte di prodotti di corrosione.Le valvole A e B sono incrinate nelle pieghe, la parte esterna della curva è lungo la valvola, la bocca dell'anello della valvola B è incrinata verso l'estremità e la freccia bianca tra le superfici incrinate sulla superficie della valvola A è contrassegnata .Da quanto sopra, le crepe sono ovunque, le crepe sono le più grandi e le crepe sono ovunque.
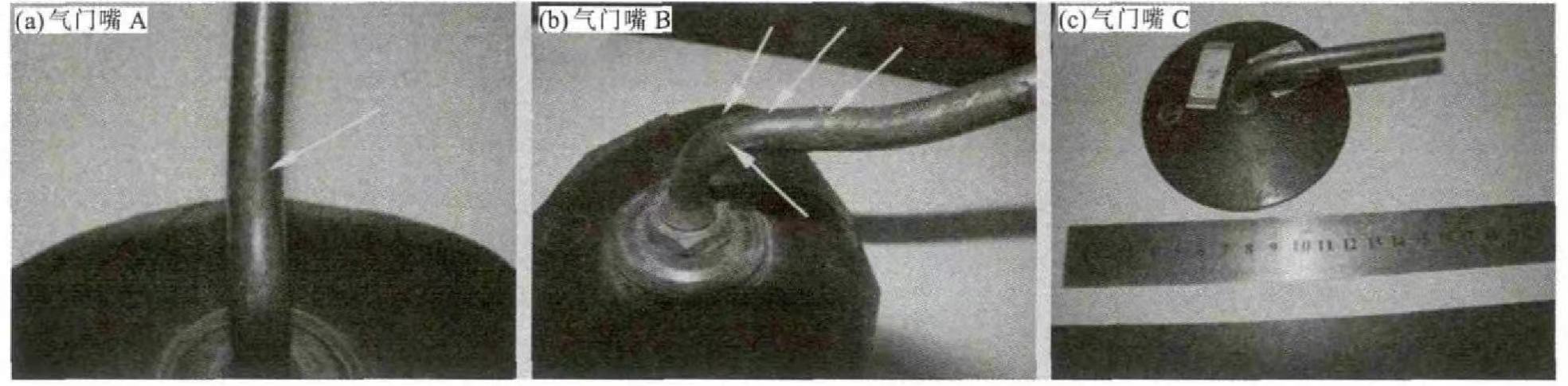
Una sezione delvalvola del pneumaticoI campioni A, B e C sono stati tagliati dalla piega e la morfologia superficiale è stata osservata con un microscopio elettronico a scansione ZEISS-SUPRA55 e la composizione della microarea è stata analizzata con EDS.La Figura 2 (a) mostra la microstruttura della superficie della valvola B.Si può vedere che ci sono molte particelle bianche e luminose sulla superficie (indicate dalle frecce bianche nella figura) e l'analisi EDS delle particelle bianche ha un alto contenuto di S. I risultati dell'analisi dello spettro energetico delle particelle bianche sono mostrati nella Figura 2 (b).
Le Figure 2 (c) ed (e) sono le microstrutture superficiali della valvola B. Dalla Figura 2 (c) si può vedere che la superficie è quasi interamente coperta da prodotti di corrosione e gli elementi corrosivi dei prodotti di corrosione mediante analisi dello spettro energetico includono principalmente S, Cl e O, il contenuto di S nelle singole posizioni è più elevato e i risultati dell'analisi dello spettro energetico sono mostrati in Fig. 2 (d).Dalla Figura 2(e) si può vedere che sono presenti microfessure lungo l'anello della valvola sulla superficie della valvola A. Le Figure 2(f) e (g) sono le micro-morfologie superficiali della valvola C, anche la superficie è completamente coperto da prodotti di corrosione e gli elementi corrosivi includono anche S, Cl e O, simile alla Figura 2 (e).Il motivo della rottura potrebbe essere la tensocorrosione (SCC) derivante dall'analisi del prodotto della corrosione sulla superficie della valvola.La Fig. 2(h) è anche la microstruttura superficiale della valvola C. Si può vedere che la superficie è relativamente pulita e la composizione chimica della superficie analizzata mediante EDS è simile a quella della lega di rame, indicando che la valvola è non corroso.Confrontando la morfologia microscopica e la composizione chimica delle tre superfici della valvola, è dimostrato che nell'ambiente circostante sono presenti mezzi corrosivi come S, O e Cl.
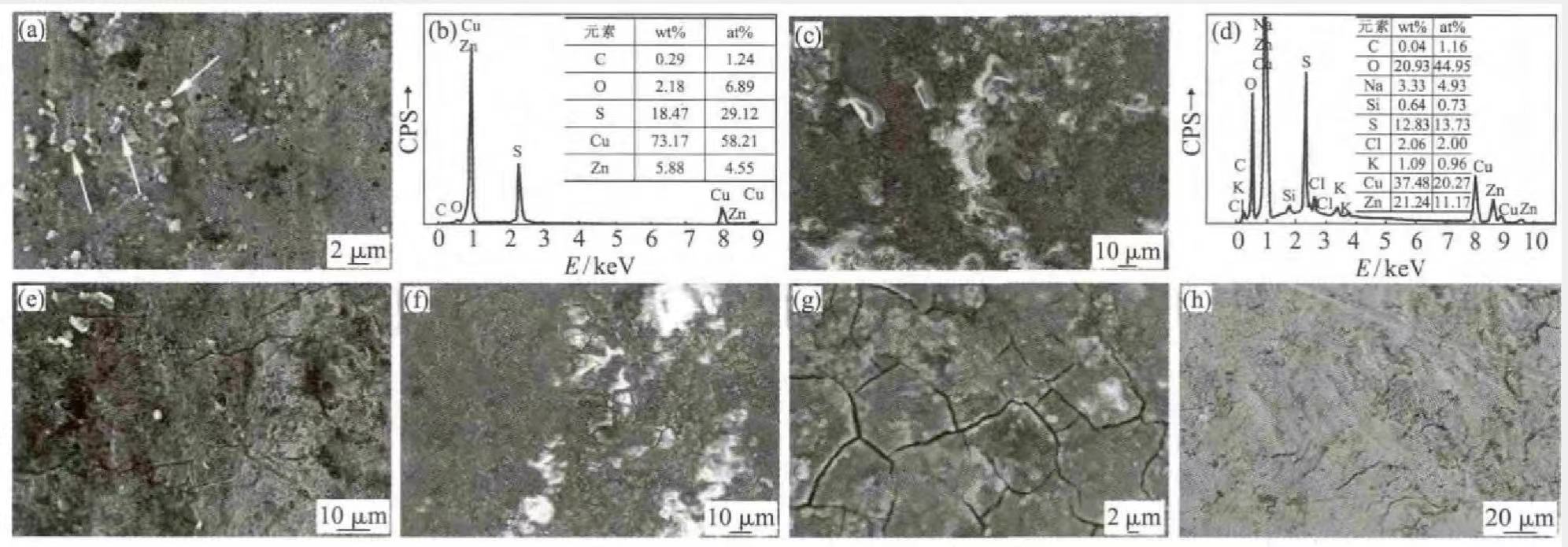
La fessura della valvola B è stata aperta durante la prova di flessione e si è constatato che la fessura non ha penetrato l'intera sezione trasversale della valvola, si è incrinata sul lato della piega posteriore e non si è incrinata sul lato opposto alla piega posteriore della valvola.L'ispezione visiva della frattura mostra che il colore della frattura è scuro, il che indica che la frattura è stata corrosa, e alcune parti della frattura sono di colore scuro, il che indica che la corrosione è più grave in queste parti.La frattura della valvola B è stata osservata al microscopio elettronico a scansione, come mostrato nella Figura 3. La Figura 3 (a) mostra l'aspetto macroscopico della frattura della valvola B.Si può vedere che la frattura esterna vicino alla valvola è stata ricoperta da prodotti di corrosione, indicando ancora una volta la presenza di mezzi corrosivi nell'ambiente circostante.Secondo l'analisi dello spettro energetico, i componenti chimici del prodotto della corrosione sono principalmente S, Cl e O, e il contenuto di S e O è relativamente elevato, come mostrato in Fig. 3 (b).Osservando la superficie della frattura, si riscontra che il modello di crescita della fessura è lungo il tipo cristallino.Un gran numero di crepe secondarie può essere visto anche osservando la frattura a ingrandimenti maggiori, come mostrato nella Figura 3 (c).Le fessure secondarie sono contrassegnate con frecce bianche in figura.I prodotti della corrosione e le modalità di crescita delle cricche sulla superficie della frattura mostrano ancora una volta le caratteristiche della tensocorrosione.
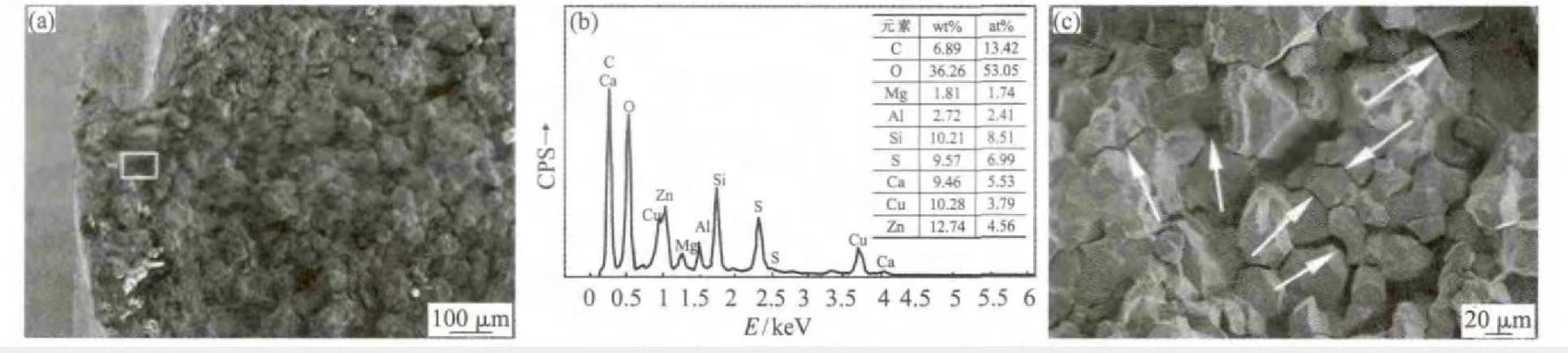
La frattura della valvola A non è stata aperta, rimuovere una sezione della valvola (compresa la posizione fessurata), molare e lucidare la sezione assiale della valvola e utilizzare Fe Cl3 (5 g) + HCl (50 mL) + C2H5OH ( 100 mL) di soluzione è stata incisa e la struttura metallografica e la morfologia della crescita delle cricche sono state osservate con il microscopio ottico Zeiss Axio Observer A1m.La Figura 4 (a) mostra la struttura metallografica della valvola, che è una struttura a doppia fase α+β, e β è relativamente fine e granulare e distribuita sulla matrice della fase α.I modelli di propagazione delle crepe nelle fessure circonferenziali sono mostrati nella Figura 4 (a), (b).Poiché le superfici delle fessure sono piene di prodotti della corrosione, lo spazio tra le due superfici delle fessure è ampio ed è difficile distinguere i modelli di propagazione delle cricche.fenomeno della biforcazione.Su questa fessura primaria sono state osservate anche molte crepe secondarie (contrassegnate con frecce bianche nella figura), vedere Fig. 4 (c), e queste crepe secondarie si sono propagate lungo la fibra.Il campione di valvola incisa è stato osservato al SEM e si è riscontrato che c'erano molte micro-fessure in altre posizioni parallele alla fessura principale.Queste microfessurazioni hanno avuto origine dalla superficie e si sono espanse all'interno della valvola.Le fessure si biforcavano e si estendevano lungo la venatura, vedere Figura 4 (c), (d).L'ambiente e lo stato tensionale di queste microfessure sono pressoché identici a quelli della fessura principale, per cui si può dedurre che anche la forma di propagazione della fessura principale è intergranulare, il che è confermato anche dall'osservazione della frattura della valvola B. Il fenomeno della biforcazione di la fessura presenta nuovamente le caratteristiche di tensocorrosione della valvola.
2. Analisi e discussione
Riassumendo si può dedurre che il danneggiamento della valvola sia causato da tensocorrosione causata da SO2.La tensocorrosione generalmente deve soddisfare tre condizioni: (1) materiali sensibili alla tensocorrosione;(2) mezzo corrosivo sensibile alle leghe di rame;(3) alcune condizioni di stress.
Si ritiene generalmente che i metalli puri non soffrano di tensocorrosione e che tutte le leghe siano suscettibili alla tensocorrosione a vari livelli.Per i materiali in ottone, si ritiene generalmente che la struttura bifase abbia una maggiore suscettibilità alla tensocorrosione rispetto alla struttura monofase.È stato riportato in letteratura che quando il contenuto di Zn nel materiale di ottone supera il 20%, si ha una maggiore suscettibilità alla tensocorrosione, e maggiore è il contenuto di Zn, maggiore è la suscettibilità alla tensocorrosione.La struttura metallografica dell'ugello del gas in questo caso è una lega a doppia fase α+β e il contenuto di Zn è di circa il 35%, superando di gran lunga il 20%, quindi ha un'elevata sensibilità alla tensocorrosione e soddisfa le condizioni del materiale richieste per lo stress fessurazione per corrosione.
Per i materiali in ottone, se la ricottura di distensione non viene eseguita dopo la deformazione per lavorazione a freddo, la tensocorrosione si verificherà in condizioni di stress adeguate e in ambienti corrosivi.Lo stress che provoca la fessurazione da tensocorrosione è generalmente lo stress di trazione locale, che può essere stress applicato o stress residuo.Dopo che il pneumatico del camion è stato gonfiato, si genererà uno sforzo di trazione lungo la direzione assiale dell'ugello dell'aria a causa dell'alta pressione nel pneumatico, che causerà crepe circonferenziali nell'ugello dell'aria.La sollecitazione a trazione causata dalla pressione interna del pneumatico può essere calcolata semplicemente secondo σ=p R/2t (dove p è la pressione interna del pneumatico, R è il diametro interno della valvola e t è lo spessore della parete la valvola).Tuttavia, in generale, la sollecitazione di trazione generata dalla pressione interna del pneumatico non è eccessiva e occorre considerare l'effetto della sollecitazione residua.Le posizioni di cracking degli ugelli del gas sono tutte nel backbend, ed è ovvio che la deformazione residua nel backbend è grande e lì è presente uno stress di trazione residuo.Infatti, in molti componenti pratici in lega di rame, le fessurazioni da tensocorrosione sono raramente causate da sollecitazioni di progettazione e la maggior parte di esse sono causate da tensioni residue che non vengono viste e ignorate.In questo caso, nella piega posteriore della valvola, la direzione della sollecitazione di trazione generata dalla pressione interna del pneumatico è coerente con la direzione della sollecitazione residua, e la sovrapposizione di queste due sollecitazioni fornisce la condizione di sollecitazione per l'SCC .
3. Conclusione e suggerimenti
Conclusione:
La rottura delvalvola del pneumaticoè causato principalmente dalla tensocorrosione causata da SO2.
Suggerimento
(1) Tracciare la fonte del mezzo corrosivo nell'ambiente circostantevalvola del pneumaticoe cercare di evitare il contatto diretto con il mezzo corrosivo circostante.Ad esempio, è possibile applicare uno strato di rivestimento anticorrosivo sulla superficie della valvola.
(2) Lo stress di trazione residuo della lavorazione a freddo può essere eliminato mediante processi appropriati, come la ricottura di distensione dopo la piegatura.
Orario di pubblicazione: 23 settembre 2022